A RESEARCHER WITH PEDIGREE IN AGRITECH
Mel Wieting has always been somewhat of a visionary in the world of agriculture. After graduating with a masters degree from Stanford in the early ‘80s, Wieting went to work for one of the premier government-backed research labs, Lawrence Livermore National Laboratory, working on technologies to predict and maximize crop yields.
After 15 years at LLNL, he was ready to set out on his own. In 2003, he and a partner started working on sensors and controllers that could monitor and control large farm-based pivot irrigation systems. The company – AgSense – blossomed into the industry leader in remote management technology, having recently been valued just shy of $100 million. Wieting has been in the agritech field ever since.
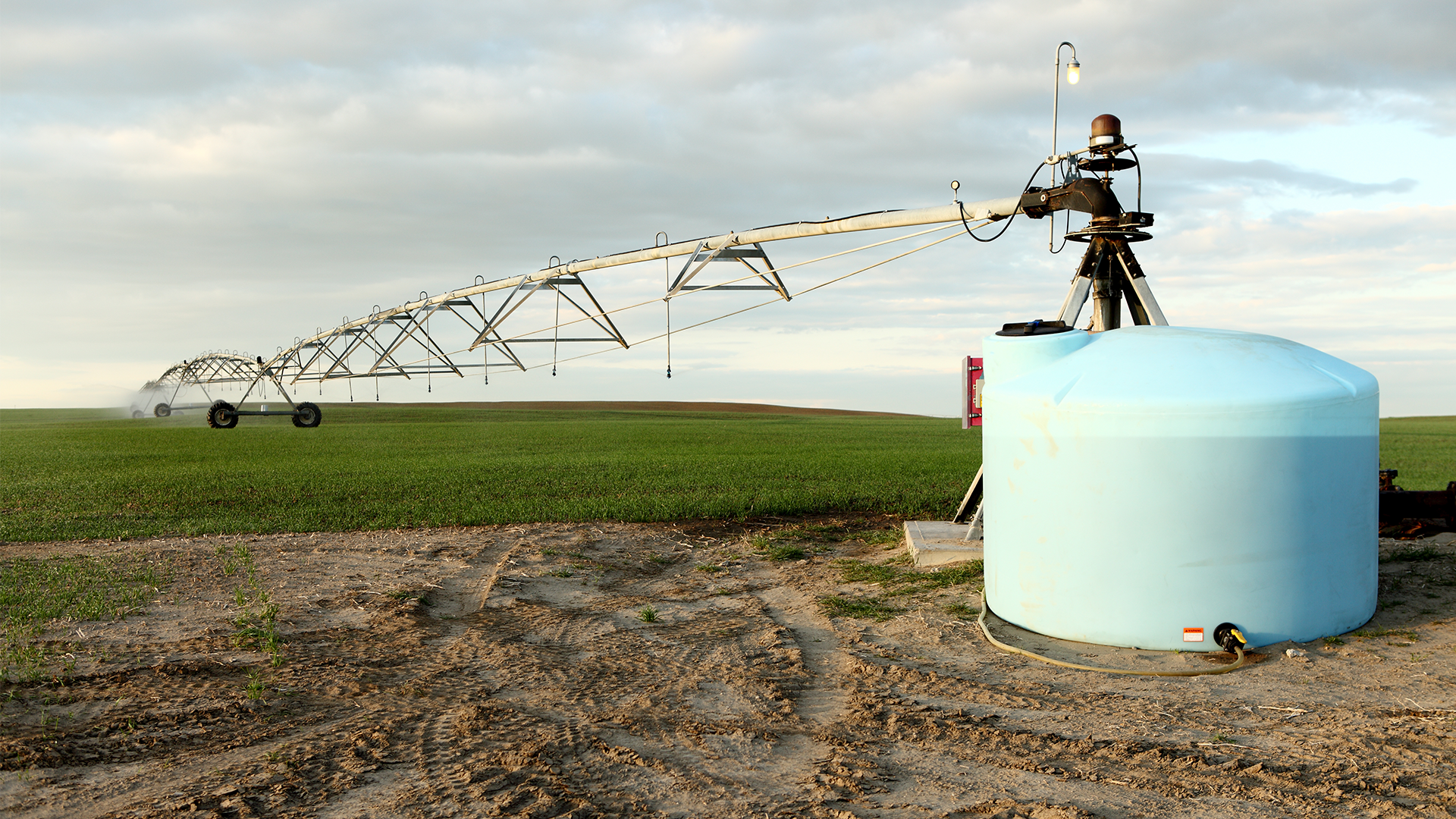
THE DRAGON TAKES FLIGHT
It was nine months ago that Wieting started his latest venture, Dragontech, with his nephew in 2020. Wieting’s nephew’s experience at large commercial farms perfectly complements Wieting’s experience in software and systems engineering and research.
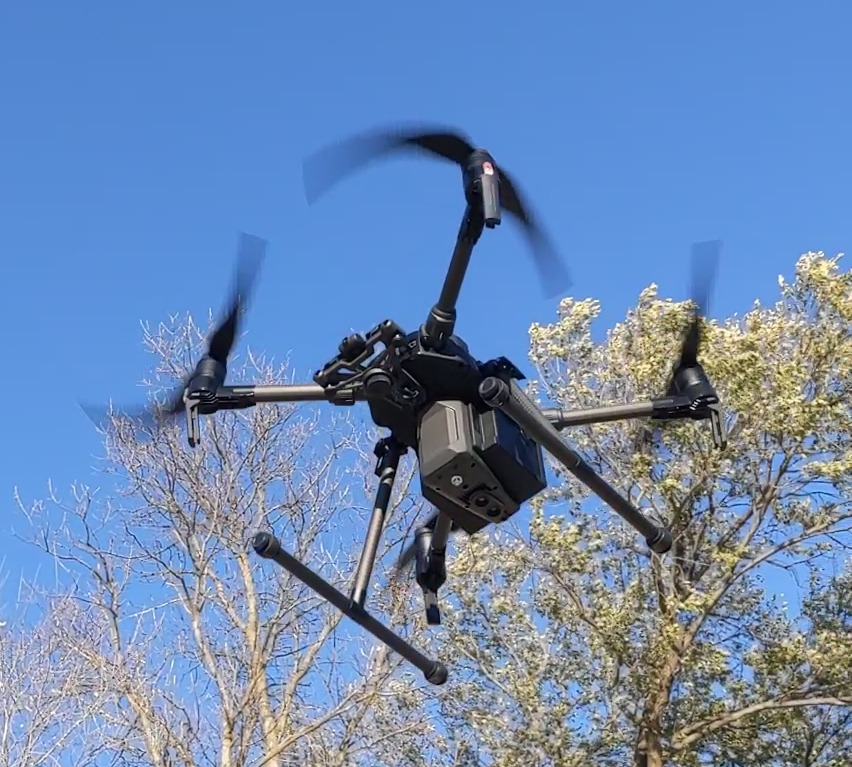
Currently, large farms have the resources to hire consultants to collect data – something Wieting is very familiar with as he has done consulting for the past nine years. The tools those consultants use are very customized packages that include, but are not limited to, drones packed with sensors. These customized packages are generally less accessible to farmers themselves, but would be extremely valuable in identifying and addressing potential problems in their fields. “We want to be able to take pretty much any kind of sensor and integrate it into a drone, and make it all integrated into a single out of the box platform so anyone can use it” says Wieting.
“There are ways that you can put together solutions now, but there’s a big potential market for a more out of box packaged solution that can cater directly to the farmers,” Dragontech aims to bring standardized solutions with customizations to the industry, making for easier and, hopefully, more widespread adoption.
DRONES + 3D PRINTERS + SENSORS = DATA
Dragontech doesn’t actually build the drones at the center of the platform, but then, in 2021 drones are pretty easy to come by off the shelf. Companies like DJI supply enterprise level drones that can carry extreme payloads. What Dragontech does is build the systems integrations.
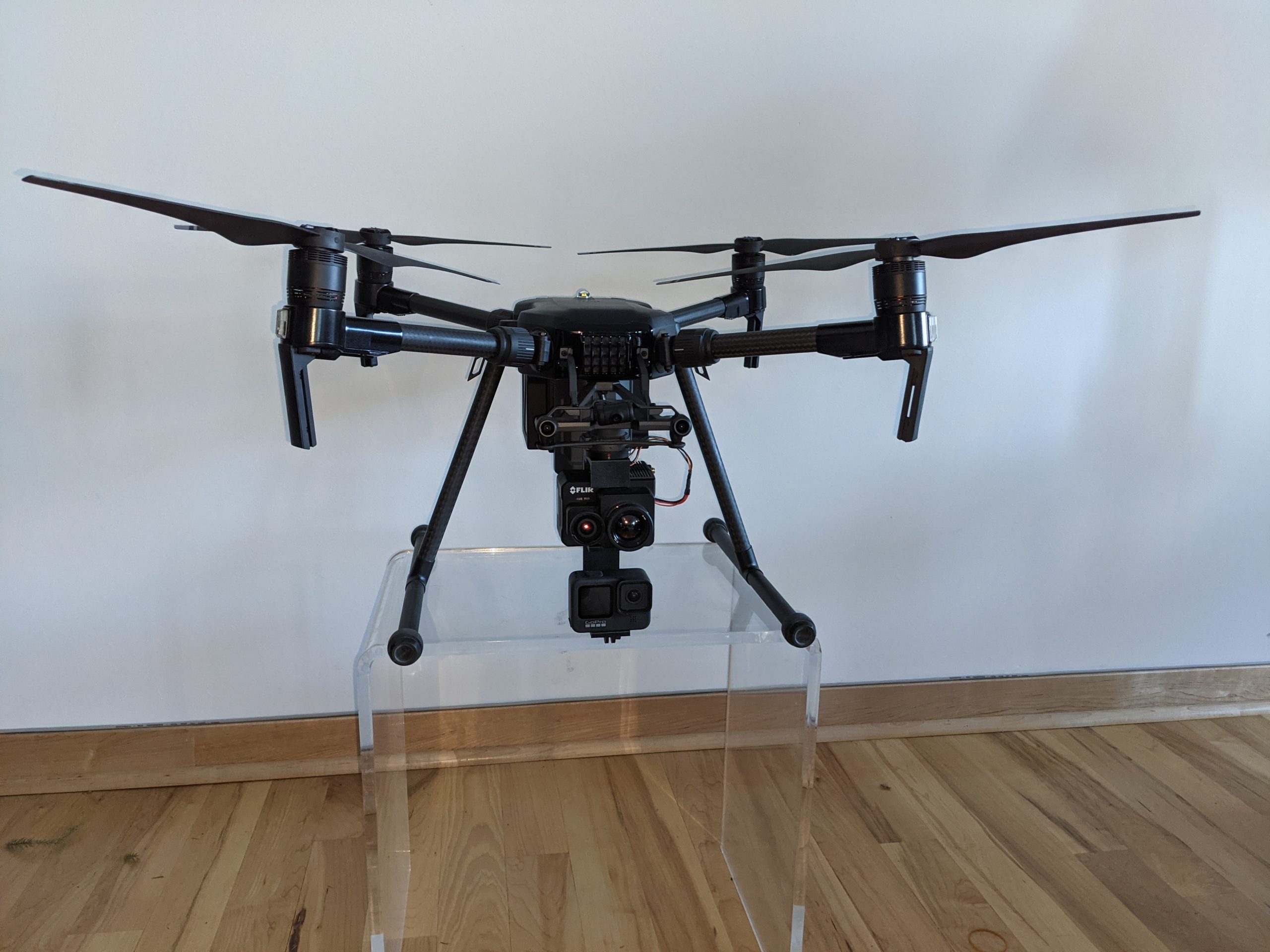
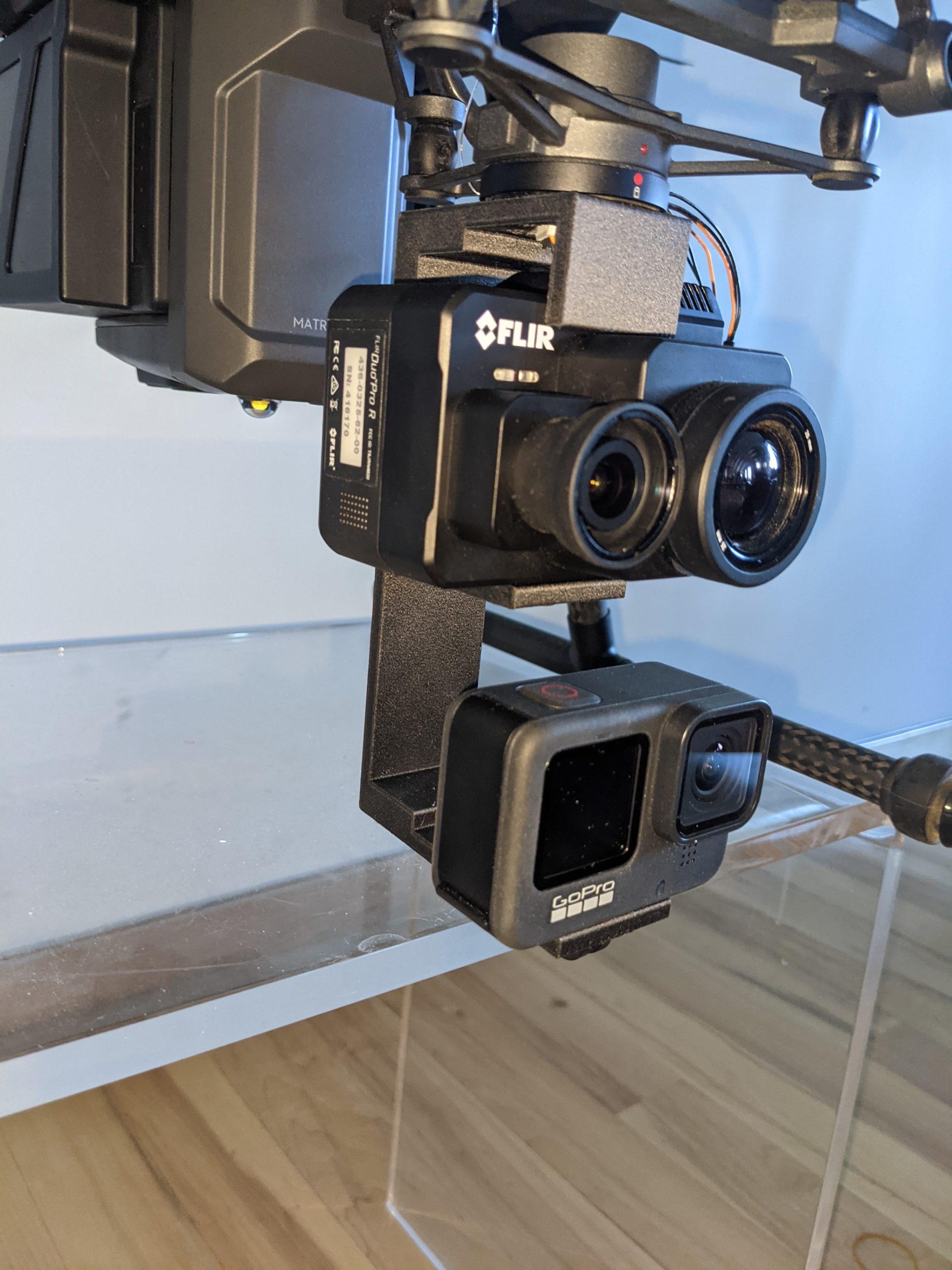
Part of the Dragontech platform incorporates the LIDAR, Multi-Spectral Spectral Sensors, and a controller attached to an enterprise drone via mounts 3D printed on the MakerBot METHOD X using Nylon Carbon Fiber.
3D printing enables Wieting to design and quickly test variations of mounts that will hold and balance these instruments. “We went out and bought a DJI enterprise drone, a few different cameras and LIDARs, and the key part of this – the METHOD X 3D printer.”
An example of one of their early builds is a DJI Matrice drone with a suite of advanced sensors (FLIR, Multi-spectral, and LIDAR), and an on board processing unit (GPU and battery) – all mounted using 3D printed Carbon Fiber brackets and fixtures. “I have some experience using 3D printers, but what intrigued me about the METHOD X was the use of Carbon Fiber material along with the enclosed heated chamber, resulting in the strongest possible parts – which is important when I’m printing fixtures to attach $10,000 sensors to a drone.”
BUILDING A LEARNING ENVIRONMENT WITHIN A BUSINESS
In 2016, Wieting teamed up with a friend to found Create Minneapolis, a STEM-forward non-profit focused on teaching kids from urban settings all about technology. His passion is clear as day when he talks about the students he works with, “[Dragontech] is important to me, but if I can help teach kids and give them access to this technology, and give them real world experience – at the end of the day that’s the most important thing.”
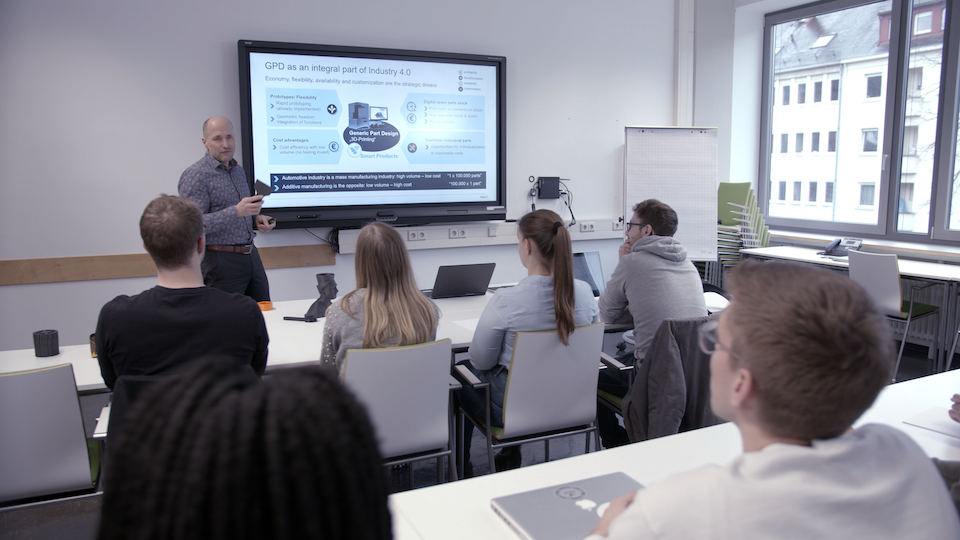
One notable synergy between his non-profit and his startup is that he can give students some real-world technical experience – including problem solving using CAD design and 3D printing – through internships at Dragontech. “We have a group of students on a robotics team and we said, ‘hey we’re starting this company – what about an internship program?’, and they were excited about that.”
The student interns who have already been using CAD design tools and 3D printing in classes or on robotics teams, bring their knowledge, but they also bring what Wieting describes as “a boundless curiosity for problem solving” – something that is not always abundant with adults.
AGILE PRODUCTION IS THE FUTURE AT DRAGONTECH
While 3D printing with the METHOD X has saved the team at Dragontech a lot of time through quick prototypes that they can test in the field, that’s not where the technology’s usefulness ends. Once Dragontech advances through their initial design and testing phase, Wieting’s plan is to create an agile production line with a digital inventory of parts,
“I can start printing [parts] right away, and I can still have them way faster than if I was using a supplier to get me the part, so it’s a massive benefit to have the printer.”
Once they have their parts vetted and optimized by an outside engineer they will create a sort of digital inventory allowing them to print parts on-demand – minimizing their requirement for outsourcing production or allocating excessive space for physical inventory storage.
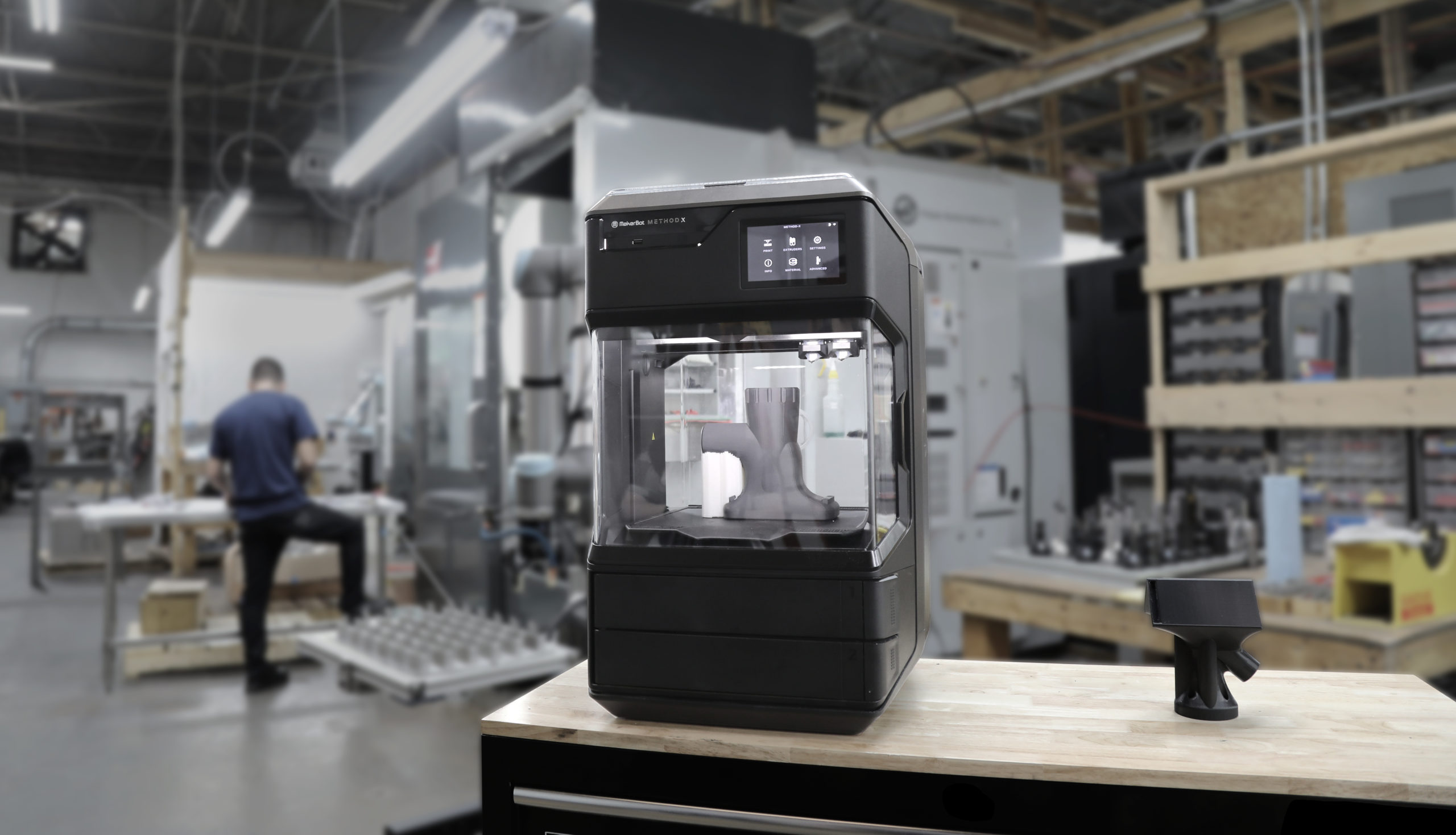
While agriculture is the starting point, Mel Wieting sees Dragontech’s potential in a variety of industries that require remote monitoring and data collection in vast environments, “We’re starting in agriculture where we see an obvious market need, but there are many other industries and applications that we could open up to in the future.”